Services
Our Services
From design to fabrication to testing to assembly and packaging
Carroll Custom Machining offers an array of services to help clients in developing the prototype that meets or exceeds proper functionality and manufacturing requirements. From design to fabrication to testing to assembly and packaging, our custom services deliver machining that fulfills component specifications and requirements. Throughout the process, we work closely with our clients, and their engineers, designers, and executives, to create the highest quality parts or assemblies to meet their needs on-time and on budget.
Our experts work closely with our clients to construct prototypes that range in size from intricate and instrument sized up to larger capabilities of 8 feet x 7 feet with a 3/4-ton lift capacity.
Design
Our custom design process develops or expands on an idea to create a working product. Whether a client comes to us with an idea or a prototype or product that needs altering, we create the drawings needed for every step of the process including prototyping, machining and assembly. We work with a variety of 2D and 3D drawing formats including DXF, DWG and 3D.
Our creative team considers many variables in developing the product design. Essential considerations are: materials to be used, environment including space and temperature, ergonomics, power requirements, testing area, and functionality of the final product.
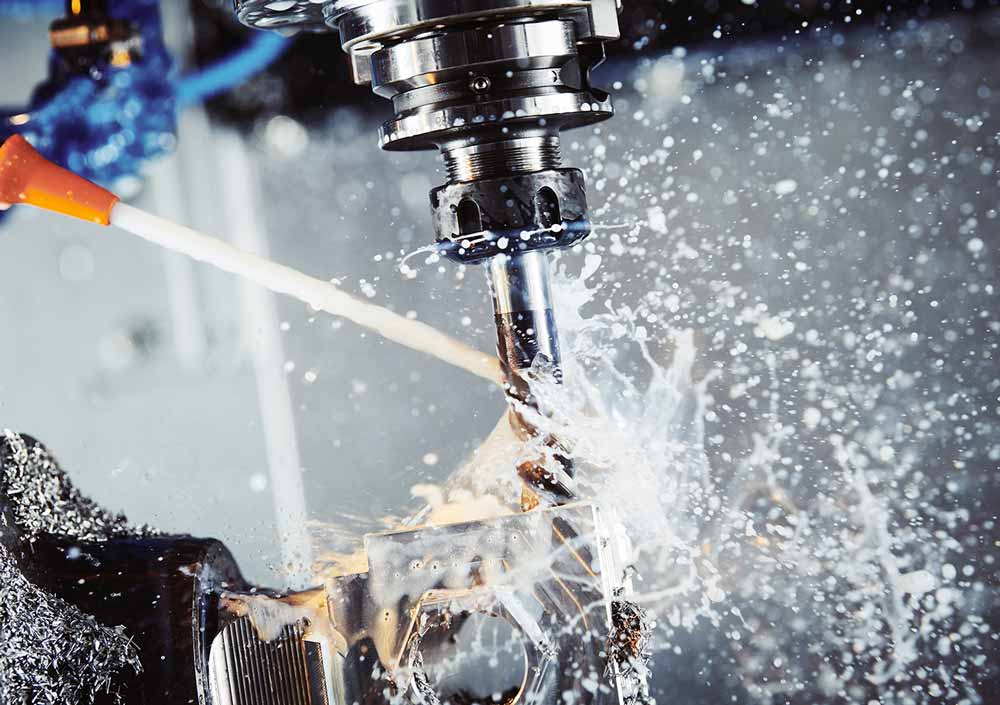
Working Drawing
The design process involves getting a workable idea on paper, culminating in the creation of a working drawing for the product.
The working drawing includes precise specifications and dimensions, drawn to scale, providing a detailed guideline for the machining process. This enables technicians to build the new product or provide alterations to an existing piece with precision and accuracy.
Prototyping
The prototyping process enables technicians to take the working design and make a basic, practical prototype for testing purposes. The prototype is built to scale or modified as requested for testing. The successful prototype enables the customer to prove a concept is ready to manufacture.
The prototype process incorporates three stages:
Proof of concept
Testing
Finishing
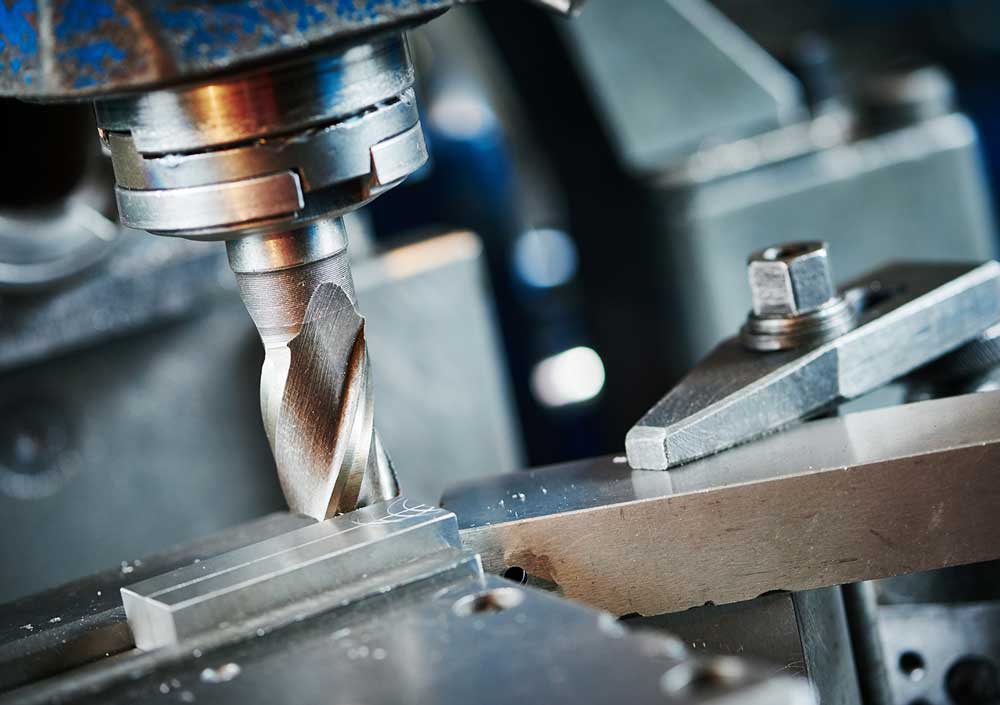
R&D
The R&D portion of the development process concerns all stages of prototyping and ultimately provides proof of functionality. During R&D, the custom designed and fabricated or provided prototype is presented for testing and modified as needed to successfully function. Technicians collaborate closely with customers to incorporate necessary modifications following testing, and prepare the prototype for additional testing. The process continues until the prototype meets intricate requirements and functions successfully.
In many cases, Carroll Custom Machining technicians and machinists also create equipment, tools or fixtures that will assist in a prototype’s assembly or testing.
Machining
The fabrication or modification of final parts occurs during the machining process,
Using lathes of 13”x40” and mills with a maximum 50”x12,” with a tolerance up to .005 inch, and if necessary, within .001 inch. This follows testing of the initial basic prototype and uses raw materials like steel, aluminum, plastic, brass, bronze and copper to create parts needed for the final prototype.
The process to create prototype parts can be computerized using 3-Axis CNC mills, run with our own customized programming, as well as lathes and grinders. Our work may also be performed manually by our machinists who are experienced in milling, grinding and other machining processes needed to craft all parts with precision and attention to detail.